ПАО «Нижнекамскнефтехим»
Предыдущие статьи:
- Как компании зарабатывают деньги. Производство прямогонного бензина
- Как компании зарабатывают деньги. Производство широкой фракции лёгких углеводородов (ШФЛУ)
- Как компании зарабатывают деньги. Пиролиз и производство этилена
- Как компании зарабатывают деньги. Производство этилбензола
- Как компании зарабатывают деньги. Производство стирола и оксида пропилена
Итак, у нас в наличии имеются бутадиен и стирол, а значит, мы можем произвести Бутадиен-стирольный каучук. ПАО «Нижнекамскнефтехим» производит его на Заводе по производству синтетических каучуков (СК) под марками ДССК-621, ДССК-628, ДССК-610. ДССК расшифровывается как дивинил-стирольный синтетический каучук.
Каучук бутадиен-стирольный марок ДССК-621, ДССК-628 предназначен для изготовления всесезонных и летних шин, обладающих низкими потерями на качение, повышенным сцеплением с мокрой дорогой и износостойкостью.
Каучук марки ДССК-610 применяются для производства современных зимних шин, обладающих низкими потерями на качение, повышенным сцеплением с обледенелой дорогой и износостойкостью.
Также выпускаются марки БС-311 и БС-2012 (БС — это бутадиен-стирольный). БС-311 используется для производства модифицированных пластиков, БС-2012 — для производства модифицированных пластиков и резинотехнических изделий.
Ещё одним продуктом, который получают из бутадиена и стирола является термоэластопласт (ТЭП) стирол-бутадиен-стирольный СБС-330. Он представляет из себя смесь из наноструктур полистирола в обычном бутадиен-стирольном каучуке.
Примерно так: шарики — наногранулы полистирола, ниточки — бутадиен-стирольные макромолекулы каучука
За счёт этого данный полимер обладает так называемой термоэластопластичностью — обладает механическими свойствами эластомера, то есть хорошо работает на сопротивление разрыву и истиранию, но при этом переходит подобно пластмассам в вязкотекучее состояние, благодаря чему его можно обрабатывать литьём под давлением. Такая комбинация свойств отлично подходит для изготовления из этого материала подошв обуви, защитных покрытий и некоторых других приложений, например как добавка к асфальтовому покрытию.
Из термоэластопластов изготавливают подошвы для таких вот КРЕМЛЕБОТОВ, например
Технология получения ДССК имеет много общего с процессами получения растворных изопреновых и бутадиеновых каучуков. Однако особенностями этого процесса являются практически полное исчерпание мономеров и, следовательно, упрощение схемы переработки возвратных продуктов; сравнительно низкий расход катализатора; высокая температура полимеризации (выше 0 °С), позволяющая использовать в качестве хладагента воду. Важно отметить, что полимеризация ДССК происходит в растворе, а не в эмульсии (что характерно для бутадиен-стирольных каучуков марок СКС) — это более редкая технология, в России по ней работают только предприятия Сибура.
Резервуарный парк на производстве ДССК. Фото ПАО «Нижнекамскнефтехим»
Шихта готовится смешением очищенных и осушенных стирола, бутадиена и растворителя (циклогексанового или гексанового).
Компоненты шихты подаются на смешение в смеситель из мерников, затем готовая шихта с помощью дозировочного насоса подается в первый полимеризатор. В этот же полимеризатор дозируют инициирующую систему, состоящую из раствора литийорганического соединения.
Сополимеризация происходит в батарее стандартных полимеризаторов объемом около 20 м3 при последовательной непрерывной подаче шихты снизу и выводе полимеризата из верха аппаратов. В полимеризаторах поддерживается температура 20°С-60°С, при этом на выходе из последнего аппарата достигается практически полная конверсия мономеров. Теплота, выделяющаяся при полимеризации, отводится промышленной циркуляционной водой, подаваемой в рубашки аппаратов.
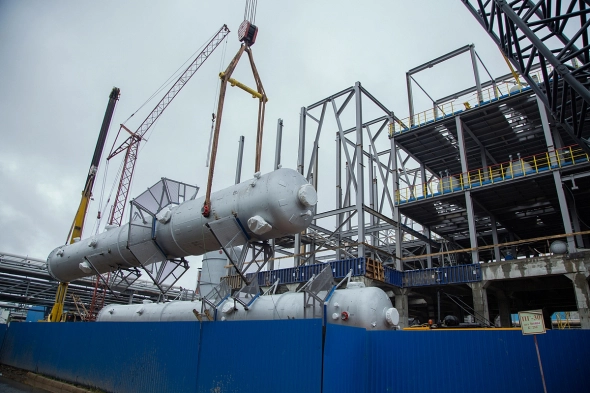
Колонны на стадии очистки растворителя были изготовлены в Башкортостане. Первая колонна предназначена для очистки растворителя от тяжелых компонентов, а вторая — для осушки растворителя от влаги, чтобы потом его подавать на узел полимеризации. Фото ПАО «Нижнекамскнефтехим»
Раствор стабилизатора дозируется на смешение с полимеризатом для дезактивации катализатора. Полимеризат через фильтр, где отделяется нерастворимый в углеводородах полимер, подается в смеситель на смешение с раствором стабилизатора. Заправленный стабилизатором полимеризат после усреднения в емкости насосом откачивается на водную дегазацию, которая осуществляется по обычным схемам, применяемым в производстве изопренового каучука, при температуре 100°С-115°С и давлении 1,5-2,0 атм. После дегазации от растворителя отделяется образовавшаяся крошка каучука.
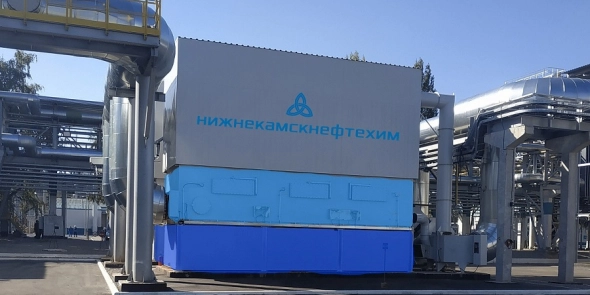
При дегазации образуется некоторое количество газообразной фазы, которую нельзя сбрасывать в атмосферу просто так. На новом производстве ДССК используют блок каталитического окисления газовых выбросов, похожий на тот, что используется на линии выхлопа автомобиля с ДВС, только побольше, как видите
При необходимости получения масло- или саженаполненного каучука (используется в рецептуре некоторых резиновых смесей) в раствор каучука перед дегазацией вводят наполнители — углеводородное масло или технический углерод (или диоксид кремния).
Дальнейшая сушка и упаковка каучука проводятся по схемам, аналогичным изопреновому каучуку.
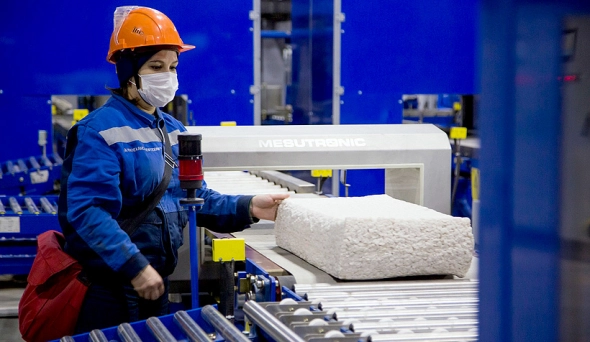
Аппаратчица нежно поглаживает тёплую поверхность брикета ДССК. Фото ПАО «Нижнекамскнефтехим»
При производстве термоэластопласта СБС процесс полимеризации проводится в две стадии: полимеризация стирола, затем — сополимеризация дополнительного объёма стирола с бутадиеном. На каждой из стадий мономеры полностью исчерпываются. Если на первой стадии температура составляет 40 °C — 45 °C, то на второй и третьей она равна 50 °C — 60 °C и 70 °C — 80 °C соответственно. Производство периодическое, цикл с откачкой из реактора составляет 90-100 мин. Процесс полимеризации длится 70-75 мин.
Дезактивацию катализатора проводят стабилизатором, например агидолом-1, вводимым в виде раствора. После дегазации термоэластопласт далее отжимают в червячном прессе, сушат в виде гранул и упаковывают.
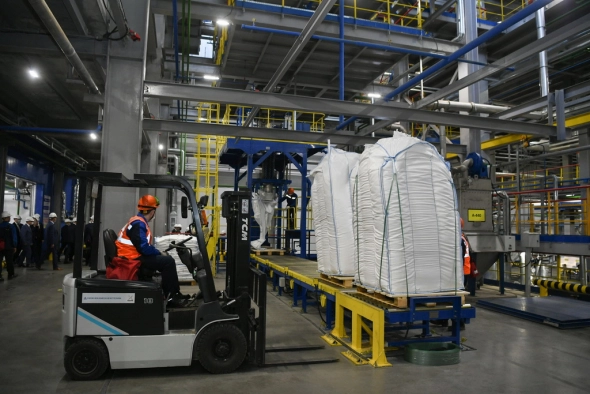
Гранулы термоэластопласта упаковывают вот в такие биг-беги
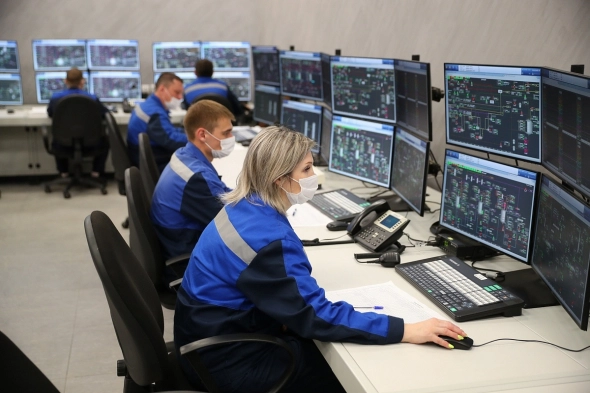
Не могу не обратить внимание, что для аппаратчиков на пульте ДССК поставили аж по четыре монитора! На предприятии, где я работаю, они обходятся двумя, а тут четыре — прям ЖЫР. Система управления, кстати, Yokogawa — узнаётся даже издалека.
Теперь о цифрах. Производство ДССК и ТЭП для ПАО «Нижнекамскнефтехим» новое — оно пущено только в январе 2021, что-то интересное могут рассказать в годовом отчёте 2021 (который красивый буклет, в МСФО-шке никаких подробностей я не увидел). Мощность производства ДССК составляет
60 тыс. тонн/год, термоэластопласта —
10 тыс. тонн/год.
Помимо Нижнекамскнефтехима ДССК производят также и на другом предприятии Сибура — «Воронежсинтезкаучук» (
14 тыс. тонн/год). Не забудем и о колыбели отечественного каучука — филиале ФГУП «НИИСК» в Воронеже, именно на опытном предприятии этого института под руководством Лебедева (
который, собственно, синтетический бутадиеновый каучук и изобрёл) были получены первые в России синтетические каучуки. Сегодня ФГУП «НИИСК» периодически выпускает малые партии ДССК под заказ или для исследований, предприятие всё-таки научное, но радует вот эта непрерывность традиций, институту скоро исполнится 100 лет. Другие российские производители ТЭП те же -- «Воронежсинтезкаучук» (
73 тыс. тонн/год) и филиал ФГУП «НИИСК» в Воронеже (малые партии).
Крупнейшие мировые производители ДССК -- Asahi Kasei, JSR, Kumho, Trinseo, Arlanxeo, Versalis, Michelin. Мировые мощности рассчитаны на производство
4,9 млн. тонн/год бутадиен-стирольного каучука. В основном (
82%) существующие мощности предназначены для производства бутадиен-стирольного каучука эмульсионной полимеризацией (марки типа СКС), доля производства каучука растворным методом (ДССК) – около
18%.
Альберт М., да и акции — неликвид.
в стакане полтора землекопа пустоту шевелят...